When I checked out Dewey's
guitar, the strings had pulled the neck into a little relief. I removed
it by tightening the truss rod 1/8th of a turn. There are two marks on the
brass acorn nut, 1 is where I had the neck adjusted straight the first day,
the other mark (at top of nut with a "2" mark behind it) is where the neck
wants to be straight today. It could be over-straight, even back-bowed when
Dewey receives it. He will have to back off the trussrod nut (counterclockwise)
to the initial mark in that case. |
|
|
I didn't
need to raise the bridge, however when I do I use this "bridge-jack" from
the old Kalamazoo factory. It takes the load and lets the thumbwheels rotate
freely, quickly. |
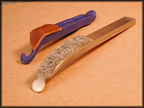 |
You can
make your own "Kalamazoo Jack" from a bicycle tire lever (for removing the
tire from the rim) with leather superglued to it. |
|
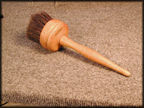 |
This
is a "bench brush" from the old Kalamazoo factory - used to brush shavings
from the bench top. At one time the bristles would have been three times
longer - it saw much use. I got from the auction when Gibson moved to
Nashville. |
|
The bridge saddles
looked like this after strobe-tuning. The A-string would never have intontated
properly faced backwards, and the E-string woulda' had a time, too. |
|
|
In
the refracted light you can see the thin finish and how it has already
shrunken into the sworled grain of the top - great look! |
|
These length-wise marks
are where the lacquer has shrunken and the factory buff-marks show as striations
- another cool look. |
|
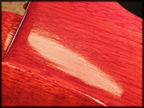
The thin finish,
and just the right filling technique, produce a very vintage-looking
"shrink-back" on the mahogany. Very cool!
|
|
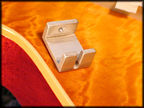 |
Here's
a little tool I made for loading Humbuckers into a mounting ring... |
|
It holds the spring
and lets you install the screw easily and without wrestling-this can be
tricky on some guitars-especially a good looking babe like Dewey's got..
|
|
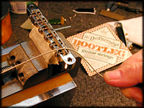 |
After seating the bridge
saddles to the radius I chose to use (using nut files), I burnished the
slots with the strings themselves..the two lower saddles are facing backwards
(ala vintage Gibson), I changed that soon.. |
|
Dewey's
fretboard radius was 12", but the bridge could not reach that radius without
alot of deep saddle slotting. I went with 15" bridge saddle radius that
was slightly flatter than the freboard itself. (Not a bad way to go as I
see it). I set the neck polepieces at 14". |
|
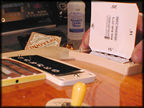 |
...and the bridge polepieces
at 15" - the strings were gradually flattening as they went to the bridge.
These polepieces are ZIG-ZAGGED, with the screwdriver slot going neither
with the line of the strings or cross-wise to it (ala Gibson 1950s-it also
gives more metal under the string to pickup the sound). OPINIONS ON THIS
ARE WELCOMED! |
|
The bridge saddles
are 15" (underneath the strings) |
|
.
|
I turned the low E-and
A-saddles forward-the spacing was dead center and allowed me to do it. I
don't think it would have reached proper intonation without this. I don't
like turning those two saddles "backwards" |
|
I set the tailpiece
up off the top a bit.. |
|
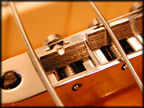 |
The only saddle I needed
to groove somewhat deeply was the low-E. |
|
With the outside E-strings
pressed down at the last fret....I set the outside E-polepieces to the factory
specs of 3/32" on the neck pickup and 1/16" at the bridge. I will further
adjust this by ear to balance the pickups to each other if I don't like
what I hear. |
|
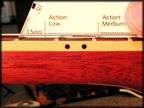 |
I set the action as
low as I could get it-I can always raise it up. With a capo at the first
fret to eliminate the nut height from the equation I set the Low-E to 3.5/64"
and the treble E at 1/32". It played good right there (quite low, but tight-and
with good tone). This tool was supposed to have been in my new book, but
the die-cutter "couldn't cut it" (as he said he could). I am looking now
for a LASER cutter to do the next printing of the book cuz I want the tool(s)
in there! |
|
This is my cool measuring
tool that wasn't! It measured fret height, fret width, string height, and
gave quick action measurements of low, medium, medium-high etc. It read
both Imperial and Metric. People would love it if the DIE-CUTTER could have
produced what he promised. (We pulled it at the last second). |
|
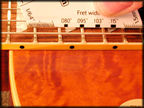
...fret width markers... |
...fret height graduations
(strings removed-hold against fret)...
|
...and even a 'lil
rule... |
|
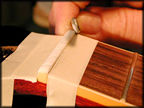 |
... I spent some time
removing all the sharp edges of the nut, lowered the top of the nut since
I dropped the strings closer to the first fret, and polished it far more
than Gibson did... |
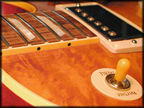 |
Dewey's frets are done,
and they look pretty good-but nothing like the beautiful wood on the top
of his R9. |
|
|
|
|