From left to right
these pots are a recent Gibson regular length shaft pot typical of what
has been in the recent Historic Les Pauls, a recent Gibson long length
shaft pot typical of what has been in the recent regular production Les
Pauls, a CTS made AllParts regular length shaft pot AllParts number EP086,
a CTS made AllParts long length shaft pot AllParts number EP686, and CTS
made for Gibson long shaft pot from the mid 1990s.
Click on Images to Enlarge
|
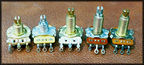
From left to right, recent Gibson short shaft, AllParts CTS short shaft,
recent Gibson long shaft, AllParts CTS long shaft, CTS made for Gibson
long shaft. Note some of the differences, the AllParts CTS short shaft
has a top portion that is some kind of cast metal instead of a piece of
stamped steel. The AllParts CTS pots have what appears to be an aluminum
shaft, as opposed to the brass shaft of the older CTS made for Gibson.
I inquired to AllParts about the shafts, they couldn't tell me much. It
could be a cost reduction or maybe for saving weight. Note that the CTS
short shaft and CTS made for Gibson pots have the four metal tabs bent
up to allow the pot to be disassembled. Note that when comparing the AllParts
and recent Gibson short shafts, the AllPart CTS pot has a small extra
portion at the end beyond the knurling. Someone noticed that if replacing
just the two volume pots in an Historic LesPaul, the knobs ended up sitting
up just a bit higher than the original Gibsons due to this little extra
at the end of the shaft. I recently installed two such pots in a friend's
Historic, but I prepared them ahead of time by taking them to a bench
power grinder and removed that extra 1/16 or so grinding the end of the
shaft level with the knurling.
|
Click on Images to Enlarge
|
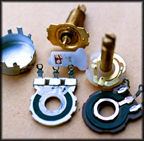
This
pic of the disassembled pots focuses on the miniature wiper of the Gibson
pot versus the heavy brass wiper of the CTS pot.
|
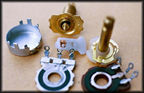
This shows the
pots further disassembled, Gibson to the left, CTS to the right. Note
the much _much_ larger brass wiper and the heavier design and construction
of the resistive element of the CTS, versus the little wiper of the
Gibson with the five tiny fingers.
|
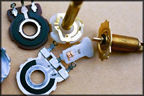
Another angle showing the disassembled pots.
|
Sobering sight... A
side view of a CTS pot versus the Gibson. Note the heavy brass wiper,
thicker resistive element, heat tolerate materials in the CTS versus the
rather wimpy little wiper, plastic guts, and minimal resistive element
in the Gibson.
|
Another pic of the
side view comparison, CTS pot versus recent Gibson.
|
Here's another pic
of the cracked Gibson pot, this time with a little commentary added courtesy
of Mayor Dave.
|
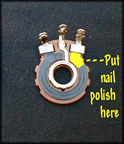
This pic illustrates
the "nail polish mod". By applying some insulation such as clear nail
polish in this area of the resistive element track, you create a tone
pot that disconnects as you turn it to full on, as you adjust from 9
to 10. Disconnecting the tone pot can help to bring out some extra response
and clarity with the higher output pickups such as the Gibson 498T or
500T, Seymour Duncan models Duncan Custom, Duncan Distortion, or similar.
More Pot Talk
The "Brian Mod"
LPF Potentiometer Discussion
More
Potentiometer Comparisons
|
|